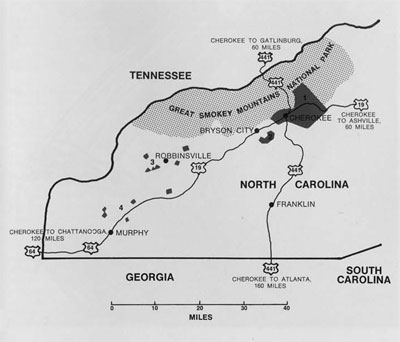
Cherokee, North Carolina did an eighteen million dollar tourist business in 1972. Much of this money went to outsiders who held leases on motels, restaurants, and tourist shops on the Qualla Boundary, land of the Corporation of the Eastern Band of Cherokee. Many of the tourists who came there to look at Indians saw little of the traditional Cherokee way of life; many bought souvenirs made in foreign lands, but some purchased genuine Cherokee craft items, such as beadwork, pottery, wood carvings, or basketry. Only those who purchased Cherokee baskets and carvings obtained traditional Cherokee crafts.
Wood carving is a vigorous Cherokee craft. Its styles have been reshaped by Mountain White models, by woodwork taught at boarding schools, and by cosmopolitan art, but its forms have evolved from aboriginal models. Some of them were household utensils, such as ladles, spoons, and dough trays which found an early outside market. Pipe carving in stone and in rhododendron root was a major tradition in sculpture, and provided cash income from outside markets throughout the eighteenth and nineteenth centuries. Naturalistic and stylized life forms in full relief have been adapted from the animal and human figurines on pipes and have carried over the strength and the grace of ancient forms into modern wood sculpture. Carving shows a history parallel to that of basketry in its development of a modern craft through the transformations and the adaptability of aboriginal and pre-Columbian folk arts.
Cherokee traditional basketry represents three distinct traditions. That in cane splints has an ancient history in the Southeast, but was not practiced in many parts of the Boundary because of distance from cane resources. It had persisted in the Birdtown area of Qualla and at the Snowbird Community in Tennessee, however, and has been re-established in all areas in recent decades. Cane basketry is particularly challenging to craftswomen because of its potential for great refinement and perfection in its execution and for elaboration of designs.

Museum Object Number: 70-9-30
The second tradition, in rods and narrow splints of white oak, is assuredly of European origin. It is also found in White communities throughout the eastern United States, Known as rib baskets in the Southern Appalachians and as melon baskets in many other areas, such oval forms are woven upon a framework of rim and handle as their essential foundations. Some older Cherokee basket makers have worked in this technique since early childhood, growing up in households where this technology was the sole basketry tradition of their family, Others first learned cane techniques or broad oak splint techniques as the exclusive tradition of their families. Some family industries included two or three of these separate traditions. At any rate, it appears that the rib basket technology had become fully established as a Cherokee cottage industry by 1820. Rib baskets were already familiar to White buyers, and thus they generally preferred these to baskets in Indian styles. The manufacture of a good rib basket is time consuming and arduous, but its efficiency is attractive. All parts of the oak log are used in making a rib basket: the heartwood is split and carved into ribs (weft) whereas the heartwood would be waste in other basketry techniques; all of the sapwood, even that from inferior logs, can be used for the narrow splints (warp). A rib basket conserves material, producing the most basket for the smallest amount of wood with the least waste. Because good oak wood is still a valuable and scarce commodity, it is best to turn it into rib baskets, even though the labor is greater.

Museum Object Number: 58-6-5.
The third tradition, in broad oak splints, is probably an aboriginal one, although most scholars would dispute this claim. Broad oak splint baskets can be made only from the sapwood of white oak logs of first quality. They are of much lighter weight than rib baskets, but are equally durable. In earlier decades they were the only baskets made in the Big Cove, the most conservative and the highest and coldest mountain region of the Boundary. Such baskets find a good market today because they are attractive, useful, and extremely durable. Obtaining suitable wood is a serious production problem.
It is generally said that it would be impossible to cut and work oak or ash into splints without metal tools. Experiments in taking out and working up oak contradict this assertion. A good stone-bladed axe, handled with skill rather than with brute force, cuts and pieces logs of the proper size as well as does a steel axe. The logs are split rather than chopped into bolts. A flint or a sandstone edge readily cuts a radial slot into the end of the log, and wooden or antler wedges (“gluts”) driven by a wood maul (“club”) quickly split the log through its length. Thus the log is split into eighths (“bolts”). Each bolt then needs a small tangential notch sawed into its end at the juncture of heartwood and sapwood; careful driving of wooden wedges then splits the heart from the sapwood, “hearting out the bolt.” The “hearted-out bolt” is then split into “sticks” through the use of sawed-in notches and the application of wooden wedges. Each stick is then separated into splints of annual growth rings by cutting tangentially into its end with a flint chip; the thin layer of wood is then peeled away while cutting lightly with the flint chip to control the split. Thus a splint is readily formed. One can expect to obtain ten to twelve splints from a good oak stick approximately one inch square.
The modern Cherokee mechanic takes a log apart with both metal and wooden tools. The tree is felled and cut up into logs with the steel axe. A radial axed-split or notch is then cut into the end of the log. It is aligned with the medullary rays of the oak log which provide a plane of weakness which will split the log in half. A steel wedge is poised into this cut and driven in with a dogwood club, starting the split. Then a wedge made of persimmon wood is inserted into the split and driven in with a club. Another wooden wedge is set and driven as the split is opened, and a series of wooden wedges are inserted and cautiously driven down to split the log in half. Halves become quarters and quarters become eighths in the same pattern. The same sequence of end-notching and splitting “hearts-out” the bolt, and then splits the sapwood bolt into sticks. Axe blades and steel wedges are expensive, so they are used gently. A steel wedge is driven with a dogwood club, not a steel sledge hammer, to conserve the wedge. One never uses a steel wedge when a wooden one will do, because wooden wedges are homemade and cost nothing but the labor of grinding them into shape on a piece of sandstone, whereas steel wedges are expensive. In this technology, steel axes have merely been substituted for stone axes in felling and end-notching; steel wedges have simply been substituted for antler wedges in starting a split, and a pocket knife has taken the place of a flint chip in starting and guiding the pull-off of splints and in smoothing and edging them, Broad splint basketry is scarcely more difficult with Stone Age tools than with factory tools. Thus broad splint basketry technology, whether in oak or ash, is a good candidate for an aboriginal industry. This question will eventually be answered by archaeological data.

One of the most difficult problems of the mechanic and craftsman has always been obtaining materials suited to a craft. Good wood is a vanishing commodity. Thus a Cherokee mechanic conserves his persimmon wooden wedges because the wood is valuable. He also avoids cutting persimmon trees because he wants their fruit as a food. Dogwood is so valuable as lumber sold to furniture factories that a Cherokee is reluctant to cut it as material for hammers or mauls. Sour-wood is a valuable timber, but the nectar from its flowers is worth even more as a food for bees; this becomes the most expensive honey produced in the Carolina mountains. Good oak wood presents similar problems in that it is scarce and that its prices are competitive.
We have many species of oak, all of them good economic woods, but only a few are suitable to basketry. The red oaks, black oaks, and live oaks are commercial timber and are valuable construction material. They can be worked into baskets, but their woven splints are fragile and non-durable. No Cherokee would use them. The white oaks are of multiple value. In earlier decades white oak was split and smoothed into shingles, a Cherokee cottage industry which brought good monetary returns but which depleted the stock of oak trees. Today the oak shingle is no longer made because the raw materials are gone. Oaks large enough for shingles, those with thick enough sapwood, no longer exist.
White oak timber used to be invaluable for ship building and as the best of cabinet makers’ woods; it no longer comes to such markets. It was the wood of coopers, and most tuns, barrels, and kegs were split, shaped, and joined from white oak. The coopers’ market today determines the price of white oak, since it is made into barrels for the aging of bourbon whiskey. Any merchantable stand of oak is so valuable for the manufacture of whiskey that no other market can compete. Cherokee basket oak brings a price equal to that of keg-wood, but comes from scattered trees not salable to the distilleries. All other markets for white oak have been priced out of competition.
Several species of white oak provide good fiber-woods for basketry. Today’s harvest is almost entirely very young stands of the common white oak, Quercus alba L. Many people objected to over-harvesting of white oaks because the acorns are sweet and edible. They provided porridge and breadstuffs for humans and mast for bears and pigs. However, very few Cherokee eat acorn soup in our age of affluence, and few bears have been spared by hunters. Pigs no longer forage in the forest. People are losing their old methods for harvesting acorns. Cherokee basket makers now cut the young white oak before the whiskey companies can get to it.
Two other species, the post oak (Quercus stellata L.) and the swamp chestnut oak (Quercus prin us L.) were never common but were universally recognized as ideal basket woods. These trees usually grow in swamps or on wet land, never become large, and have dense, straight, strong sapwood which provides perfect material for broad splint baskets. Few baskets have been made of this wood because of its scarcity. Anyone hesitates lo cut these oaks for wood because their acorns, though tiny, are very sweet and nutritious. The seeds are more valuable than the lumber. Their acorns used to be called “cheese nuts” in Georgia.

Museum Object Number: 70-9-25.
(bottom left) Basketry tray of white oak splints with hickory bark binding on rim, used in winnowing and handling cornmeal and other grains. Used in Big Cove community before 1930.
Museum Object Number: 46-6-95A.
(right) Fish basket of oak splints, used by Carl Standingdeer in 1940. Earlier fish baskets have a narrower neck and a more bottle-like shape, while later ones are more cylindrical. They were used with a tiny hook and live bait in angling for brook trout. A fish basket should be just large enough to hold fish for one family meal.
University Museum Collection
Thus any Cherokee fortunate enough to have such oaks growing on his property conserved them, refused to cut them for basket wood, maintaining them as a food resource. However, most are now gone, cut and stolen by trespassers who took them to sell. Persimmon, holly, walnut, and other valuable timbers have likewise been stolen from people who sought to protect and conserve these beautiful materials. Ginsing and golden seal, the most valuable roots of commerce, have also been plucked out of the land of their protectors. In a crowded modern world of commercial values, few persons can conserve the resources of their ancestral land, nor can they control the commercial competition for craft materials. Prices for usable white oak and cane have become oppressive to the crafts person.
Most oak is harvested on the Boundary. Individual Indians have possessory holdings of tribal land. Some are fortunate to have oak. Disagreement exists as to whether there is enough oak available on tribal land to supply needs. Many of the oaks on the Boundary show signs of having been notched slightly- with an axe; this is certain evidence that they have been tested and found unsuitable for basket material. Anyone seeing such a scar will pass by the tree.
Many women do not find it worthwhile to travel long distances for suitable oak which must be purchased, cut, and transported. Instead, they prefer to buy logs from dealers who deliver materials on order. At least one of these suppliers is a White businessman from Bryson City. The going rate for a log varies; some pay $1.25; others pay less. The grain of the log is carefully examined before it is purchased.
Women faced with shortages of oak have sometimes turned to other materials such as willow or maple. Willow baskets made by Cherokee women are scarce; most of those seen in shops on the Boundary are imports from the Mediterranean. As early as 1918, at least one Cherokee woman was experimenting with maple. At the time she was pregnant and was unable to travel the distance nor to perform the physical labor necessary to prepare oak. Maple is inferior to oak as a basketry material because it is not durable. Because of its inherent weakness it has been left largely untouched on many areas of the Boundary. Thus, it is plentiful and women have increasingly turned their attention to it. It takes a dye well and results in brighter colors than one finds on oak. Thus, it catches the eye of tourists. Furthermore, less energy and strength are required to prepare the splints. Since fewer hours are spent in preparation, the sale price of a maple basket may be slightly lower than that of an oak basket, or since the maple basket appeals to tourists, it may sell for the same price as its oak equivalent. Thus, an Indian woman working totally in maple may show more profit per hour than her counterpart working in oak. One craftswoman began adding decorative maple loops to oak broad splint baskets; the frills are inserted into the basket after the weaving of warp, weft, and handle is completed. The baskets resemble Easter baskets sold commercially in most parts of the Eastern United States, but the technique was probably borrowed from Iroquois basket makers in New York state. The woman hopes to retain most of the strength of the oak while increasing the appeal of her baskets. Women recognize that the frills are nearly impossible to protect from dust and that the maple loops will break off long before the basket is worn out. Insertion of the loops or frills unavoidably weakens the strength of the weave. Nevertheless, other craftswomen, noticing the popularity of such baskets and the praise they bring, are tempted to follow the innovator’s example. The average tourist is attracted to the bright colors and the apparent skill in attaching the intricate loops. They do not realize that such a basket is less durable than the less decorative broad splint oak basket. Perhaps it would not matter to them even if they knew, since most baskets purchased by tourists are destined to become show pieces rather than utility baskets. Of all the baskets made at Cherokee the well constructed broad splint oak basket is the most able to take heavy use. If protected from dampness or carefully dried to prevent mildew, such baskets may remain in almost constant service for many years.

Museum Object Number: 74-24-6.
(bottom) Lucy George weaving a waste basket of honeysuckle runner and white oak splint.
Some women, not wishing to undertake tedious work with oak broad splints, have turned to Japanese honeysuckle. This vine was introduced to North America by, William Bertram in the late eighteenth century and is found on much of the Boundary. The material can readily be obtained and prepared by a woman. The vine runs on the ground and can be easily cut with a pocket knife. It is then tied together and put in a pot to boil. Following this, the bark can be rubbed off with a rag. The vines are then washed in cold water and are dried thoroughly before they are dyed. A few women use oak ribs for warp and honeysuckle for weft. They produce baskets which sell for approximately one third as much as rib baskets of oak. The honeysuckle basketry technique was introduced from Virginia in 1926. Because of the ready source of materials and the ease in preparation and working of the vines, honeysuckle weaving was taught to girls in their first three years of boarding school. Thus, those who had not grown up surrounded by other forms of basketry, were first initiated to the craft through the use of honeysuckle in the school. Wall pockets and mats of honeysuckle are popular tourist items. They appeal to the tourist who wants a souvenir but is unwilling to pay the price of baskets made in oak or cane. A few of the youngsters introduced to honeysuckle weaving in the elementary school have continued working in this technique. A few others took advanced basketry courses and learned to work with oak.
Due to lack of river cane near the Boundary, men go long distances to obtain it. The nearest usable cane is found at Murphy, North Carolina, but some basket makers complain that the joints of this cane are too close together, and that it does not make good baskets. Cane is not a mountain plant; it does not thrive in highland environments and is difficult to raise on the Boundary.
Several men are in the business of working part-time to obtain cane and oak for women who make baskets. One Cherokee man uses a truck and a rented motorboat in traveling 175 miles to obtain cane in Tennessee. He is in partnership with another man from the Boundary who owns a truck. They say that when the area is flooded by a proposed dam, they will cut cane at Charlotte, North Carolina.
If a crafts worker is using cane, she is able to obtain four slender strips from a stalk. She must cut precisely, easing her way through the joints and buds which occur approximately every eight inches, or the splint will break and be useless. She must also gather dye stuffs and spend several hours boiling her splints in dye. Once the splints have cooled, she is prepared to begin weaving. Dry splints must be moistened or soaked to make them pliable.
The earliest archaeological evidence for cane basketry is more than 2000 years old. All early ethnographic examples in cane were dyed. In the nineteenth century oak and cane baskets were made for trade. Nineteenth century technology at Cherokee includes both Mountain White and Indian traditions, The Mountain White rib baskets of oak, made partly from heartwood, had been fully incorporated into Cherokee technology. Indian traditional baskets of oak and cane included hominy sieves, trays, fish creels, and pack baskets. The art of making double-weave baskets from cane was lost by 1896.
Mrs. Lottie Stamper learned about double-weave baskets in 1940 from an anthropology student, Virginia Hunter, who supplied data on Houma baskets from Louisiana and showed Mrs. Stamper photographs of a British Museum specimen, which was a Cherokee double-weave basket of the 1750’s. Mrs. Stamper figured out how to make double-weave baskets and demonstrated the technique to a number of other women. Several basket makers now produce widely admired double-weave baskets.

Most women hunt for natural dyes. Qualla Arts and Crafts Mutual, Incorporated, known locally as the Qualla Cooperative, or the Coop, pays less for baskets colored with commercial dye, thus discouraging its use. Women rely heavily on walnut bark or walnut root and butternut root. Yellow root (Zanthorhyza) has been nearly exterminated on the Boundary; some say that it fades more readily than other natural dyes. Bloodroot (Sanguinaria) must be obtained during the spring when the plant can be seen. It can be stored in the ground in sand, but this technique is nearly lost. Women report difficulty in re-locating the bloodroot and frequently discover that insects have destroyed it. Increasingly they have turned to dried bloodroot which is easier to preserve. The Qualla Cooperative sells dried bloodroot and also sells handles at cost.
Men frequently obtain materials, carve handles, take baskets to markets, and bargain over prices. However, I know of only one man who was regarded as a skilled basket maker. At Cherokee basket making is the work of women. Skill is involved in weaving baskets; achieving symmetrical designs demands foresight and careful measuring; producing a basket which is firm and not lop-sided requires practice, A number of girls in their teens are good basket makers. Some complain that basket making is hard work or breaks their fingernails, but basketry is a popular high school elective. Some girls recognize it as a way to earn pocket money. I know of one teen-ager who bought her car and supports it from money made selling baskets, and of three others, still in their teens, who have small children and rely on basketry as a major source of income. Except for the very young or very old, some from all age groups find it financially worthwhile to carry on the tradition.

Museum Object Number: 29-175-710.

Museum Object Number: 46-6-49A and 46-6-49B.
The types of baskets being made reflect changing markets. In the nineteenth and early twentieth centuries, basketry was a cottage industry. Women sold baskets to local storekeepers for $.50 to $3.00. The baskets sold were utilitarian, They were mainly market baskets, but some were sieves, winnowing trays, fish creels, pack baskets, and clothes hampers. By the 1920’s new basket types were being made. Honeysuckle technique was introduced from Virginia in 1926. Since 1940 market baskets have become elongated and have acquired interlocked oak handles. Pack baskets and clothes hampers became waste baskets. Other old types are no longer made. The wood basket of the 1920’s has become the magazine basket of the 1960’s and 1970’s. Mountain White rib baskets and cane market baskets are modified into pocketbooks. Wall pockets and honeysuckle baskets and mats, as well as miniature oak baskets, are sold to tourists for much less than the twenty to forty dollars a standard basket would normally bring. Cane baskets, particularly double weaves, and large cane mats sell for much more. Miniature cane baskets are difficult to make. The few that are made are show pieces, demonstrations of skill, not made for the tourist trade.
There is a delicate balance between what the tourist will pay and what the craftswoman can receive for her efforts. The baskets must move, if she is to make a profit. At the Cooperative shop, a woman normally receives half the sales price of her basket, according to its manager. In addition, members own shares and receive dividends. These are not paid by other shops. Most crafts workers agree that selling baskets there brings the best price, although some say that it pays more only when it needs certain types of baskets. The tribe estimated that in 1972 the combined sales of crafts in other shops on the Qualla Boundary equalled craft sales at the Cooperative.
Some well-known basket makers take orders and occasionally sell baskets to tourists who seek them and make requests. A woman in this enviable position sells a basket for half again as much as the Qualla Cooperative would pay; thus, the basket maker earns more than the Coop pays, and the buyer also saves money and has the pleasure of meeting and talking with the craftswoman.
Three fine basket makers demonstrate their work at the Oconoluf tee Indian Village Museum, where they receive wages plus a commission on their baskets. One of these women has been asked to be in a movie on basketry as part of an oral history project of a Florida college. She also gives classes in basketry in Gatlinburg, Tennessee. Two of the three women have set up demonstrations at the Coop. One won a prize at the Cherokee Fair a few years ago for innovative material used in basketry; her entry was made of basswood bark. These women are justifiably proud of their baskets.

Museum Object Number: 46-6-47.
Qualla Arts and Crafts Mutual, Incorporated, was established in 1946. Initially it operated on a small scale with Mrs. Gertrude Flannigan of the Home Economics Department of the Cherokee High School (BIN packaging and shipping sales items. A conference room in the 131A agency became the sales area. In the early 1950’s a small sales area was set up in the tribally owned Boundary Tree Motel. In those days $100. in sales made a big day according to Betty Ann DuPree, present manager of the Cooperative.
The tribe gave the Qualla Cooperative land. They built a modern building in which to sell crafts and are now planning an extension. In 1971, according to tribal reports, total sales amounted to $121,179 with $68,618 being paid out to members for their craft items and dividends. There are currently 260 members, some of whom are sixty-two years old and are therefore drawing out equity shares. Approximately 150 members are ac tively producing craft items. Of these an estimated sixty-five are basket makers. The youngest member, who made baskets, was seventeen years old in 1975.
Those eligible to apply for membership in the Cooperative include Cherokee on the tribal roll and Indians married to Cherokee on the roll. Candidates submit five pieces of their best work to be evaluated by several members of the Qualla Cooperative executive committee. Members on this committee excel in various crafts; each is recognized for his particular craft on the Boundary and in some cases nationally. The Qualla Cooperative encourages standards of excellence in crafts.


Despite this, the basket making of today is probably not equal to that of past years. Craftswomen produce baskets as rapidly as possible to meet the demands of tourism. They make a larger number of inexpensive baskets because these sell well and yield more profit than larger baskets. They make more rib baskets because this enables them to use the heartwood which would otherwise go to waste. They turn increasingly to maple because it is abundantly available and makes a pretty basket; yet they recognize that maple baskets do not have the strength of oak. They put decorative maple loops, which do not last, on oak baskets, since the frills appeal to tourists. Thus, the tourists, who keep the craft alive, contribute to its defects.
Cherokee respond to market pressures. To make baskets appear functional, they give them utilitarian names such as pocketbooks or letter holders. They know a tourist is more apt to buy a basket if she can think how to use it. However, they privately wonder how many people pay thirty dollars for a waste basket and use it to hold trash.
Thirty years ago when basket prices were low and people were beginning to travel increasing distances for materials, the craft seemed doomed. But no one fully predicted the development of major highways leading into Cherokee and the resulting tourist boom. Tourism thrust Cherokee into a cash economy. Basket prices have only kept even with inflation. In 1946 a woman received approximately a day’s wage by local standards for a well-constructed oak basket: By today’s standards a Cherokee woman still receives approximately a day’s wages for such a basket. However, since she can sell many more baskets, she receives many more days’ pay than she could have in 1946. Women can now sell baskets to the shops and Cooperative in the off-seasons, thus having a year round income. For the first time it may be possible for a woman to make a living for herself and her family through basketry. Thus, the balance between increasing costs of scarce supplies and improved markets has actually tilted in favor of the basket maker and in favor of the craft’s survival.